Lubricants must be formulated to meet the requirements of the application. Consequently, they consist of a base product to which additives are added to improve the properties of the base lubricant. Although the variety of additives used in the industry is very wide, it is possible to group them into three broad categories: those that modify the properties of the lubricants, those that protect the base lubricant and those that protect the working surfaces.
Additives that modify the properties of lubricants:
● Pour point depressants and viscosity index improvers are high molecular weight organic compounds such as polyisobutene, polymethacrylates or olefin copolymers, which have long molecular chains. They allow working over a very wide temperature range while keeping their viscosity with a minimum change.
● Freezing point depressants: they act by lowering the melting temperature. The most commonly used at present is the polymeric type.
● Friction modifiers: depending on the application, a large or small difference is required between the static and dynamic coefficients of friction between alternately contacting oil-lubricated parts.
● Surfactants and emulsifiers: reduce the surface tension of a liquid. A wide variety of surfactants can provide secondary properties such as stabilisers or foaming agents.
Additives that protect the base lubricant to increase its stability are:
● Antioxidants: when a lubricant comes into contact with air, it inevitably oxidises, with a certain speed that basically depends on the characteristics of the oil and the temperature. In addition, this process can be accelerated if there is contact with some metals that act as a catalytic agent, or by the presence of contaminants in the oil, such as water, dirt and particles. Oxidation reactions lead to progressive oil degradation with the formation of soluble (weak acids) and insoluble compounds (sludge, lacquers, carbonaceous deposits). Antioxidants are compounds capable of retarding or preventing oxidation processes, i.e. improving their resistance to ageing, such as phenols, amines or organic compounds containing sulphur and/or phosphorus.
● Defoamers: In working conditions, the presence of air leading to the formation of foam is common. The presence of foam leads to a reduction in lubricating power, a decrease in cooling capacity and an acceleration of lubricant oxidation processes. Defoamers are compounds, usually based on silicones, fatty esters and high molecular weight hydrocarbons, which reduce the surface tension of the bubbles and facilitate their breakage.
● Biocides and fungicides: control microbial and bacterial activity in lubricants. Some of the most commonly used biocides are triazines, phenols and formaldehydes. Additives that protect working surfaces.

Additives that protect working surfaces
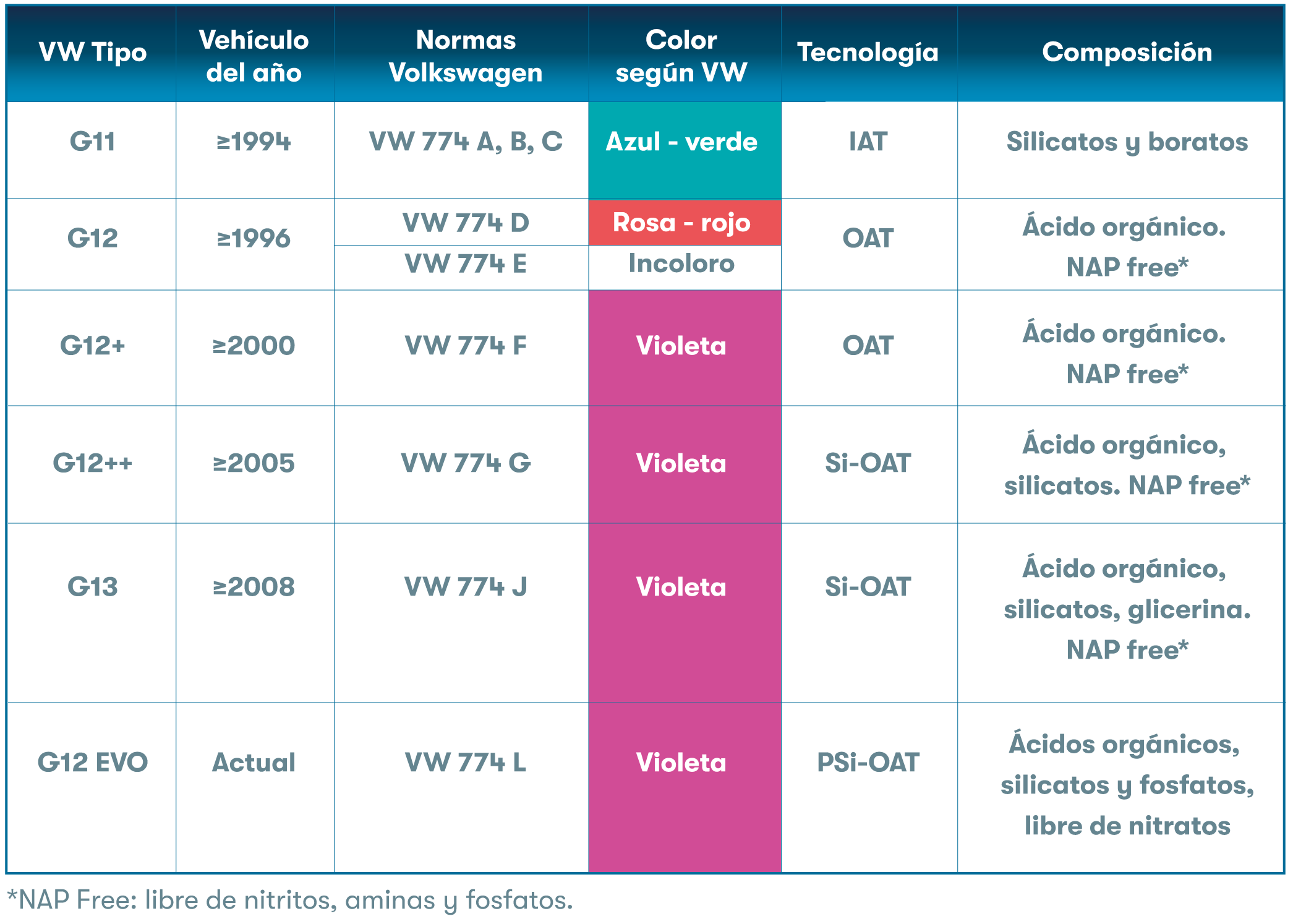
● Corrosion inhibitors: protect metal surfaces that are susceptible to corrosion due to the presence of water and oxygen by forming a protective layer. Some of the most common compounds are amines and their derivatives, carboxylic and polycarboxylic acids, borates, fatty acid alkanolamides and imidazoline derivatives.
● Anti-wear (commonly called AW additives): they form a protective film by physical or chemical adsorption that prevents welding of metal surfaces by breaking down the lubricating layer. Anti-wear additives are compounds, such as polar organic acids or zinc thiophosphates, whose chains adhere and orient themselves perpendicularly to the metal surfaces, thus forming a thin film that resists shear forces.
● Extreme-pressure (commonly called EP additives): prevent micro-welding of the two surfaces in contact when very high loads are present, as in the case of gears. The main extreme pressure additives are chlorine, sulphur and/or phosphorus-based compounds and sodium calcium sulphonates.
● Detergents and dispersants: these are polar organic compounds that prevent the agglomeration of insoluble contaminants and prevent residues on metal surfaces by keeping insoluble products in suspension as finely divided particles.
How are industrial lubricants made?
In industry, optimised lubricating oils are essential to ensure efficient production and prolong equipment life. But have you ever wondered how these industrial lubricants are made? In this article, we’ll reveal the key steps in the manufacturing process.
It is important to note that each manufacturer may have its own variant on the production process, adapting it to its specific methods and technologies. However, these general steps provide a clear picture of how industrial lubricants are produced and the care required to produce quality products.
In conclusion, industrial lubricants are the result of a meticulous process that combines careful selection of raw materials, precise mixing, quality testing and packaging. Optimum quality lubricants are essential to keep equipment running and to ensure efficient production in industries. During this process, it is ensured that the containers are clean and hermetically sealed to avoid any contamination or deterioration. In addition, they are labelled with relevant information, such as the type of lubricant, technical specifications, instructions for use and safety precautions.